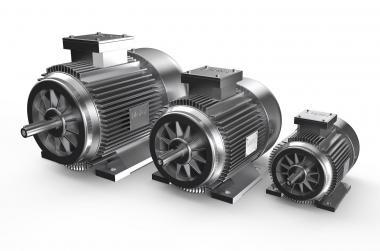
Moteur stationnaire
Bien que l'ère romantique de la vapeur soit révolue depuis longtemps, nous manquons l'ancien temps où l'on pouvait voir des wagons tirés par d'énormes locomotives magnifiques, des rouleaux compresseurs chauffés au rouge pétrissant les gravats de la route ou des locomotives fumantes travaillant dans les champs.
Une seule machine à vapeur stationnaire utilisée pour entraîner de manière centralisée, au moyen d'un système d'entraînement par courroie, toutes les machines ou métiers d'usine. Sa chaudière brûlait du charbon ordinaire.Il est peut-être dommage que nous ne verrons pas de telles machines à l'extérieur du musée, mais il est possible de construire un modèle en bois d'une machine fixe. к c'est un grand plaisir d'avoir un tel mobile en bois à la maison, un appareil de travail mobile. Cette fois, nous allons construire un modèle de machine à vapeur synchronisée à glissière plus complexe qu'auparavant. Pour conduire le modèle en bois, bien sûr, nous utiliserons l'air comprimé d'un compresseur domestique au lieu de la vapeur.
Travail à la machine à vapeur il consiste en la libération de vapeur d'eau comprimée, et dans notre cas d'air comprimé, dans le cylindre, puis d'un côté, puis de l'autre côté du piston. Il en résulte un mouvement de coulissement variable du piston, qui est transmis par la bielle et l'arbre d'entraînement au volant. La bielle convertit le mouvement alternatif du piston en mouvement de rotation du volant. Un tour du volant s'effectue en deux temps de piston. La distribution de la vapeur s'effectue à l'aide d'un mécanisme coulissant. Le temps est contrôlé par un excentrique monté sur le même axe que le volant et la manivelle. Le tiroir plat ferme et ouvre les canaux d'introduction de vapeur dans le cylindre, et permet en même temps d'expulser la vapeur détendue utilisée.
Outils: Scie Trichinella, lame de scie pour métal, perceuse électrique sur pied, perceuse montée sur établi, ponceuse à bande, ponceuse orbitale, dremel avec accessoires bois, scie sauteuse électrique, pistolet à colle à colle chaude, forets de menuiserie 8, 11 et 14 mm. Des grattoirs ou des limes à bois peuvent également être utiles. Pour piloter le modèle, on utilisera un compresseur domestique ou un aspirateur très puissant dont la buse souffle de l'air.
Matériaux: planche de pin de 100 mm de large et 20 mm d'épaisseur, rouleaux de diamètre 14 et 8 mm, planche de 20 par 20 mm, planche de 30 par 30 mm, planche de 60 par 8 mm, contreplaqué de 4 et 10 mm d'épaisseur. Vis à bois, clous 20 et 40 mm. Vernis transparent en spray. Graisse de silicone ou huile de machine.
Base de la machine. Il mesure 450 x 200 x 20 mm. Nous allons le fabriquer à partir de deux morceaux de planches de pin et les coller ensemble avec des côtés plus longs, ou à partir d'un morceau de contreplaqué. Toutes les irrégularités sur la planche et les endroits laissés après la coupe doivent être bien lissés avec du papier de verre.
Support d'axe de volant. Il se compose d'une planche verticale et d'une barre qui la recouvre par le haut. Un trou pour un axe en bois est percé au point de contact de leurs surfaces après leur vissage. Nous avons besoin de deux ensembles d'éléments identiques. Nous avons découpé des supports dans une planche de pin de dimensions 150 sur 100 sur 20 mm et des rails d'une section de 20 sur 20 et d'une longueur de 150 mm. Dans les rails, à une distance de 20 mm des bords, percez des trous d'un diamètre de 3 mm et alésez-les avec un foret de 8 mm afin que les têtes de vis puissent facilement se cacher. Nous perçons également des trous d'un diamètre de 3 mm dans les planches sur la face avant afin que les planches puissent être vissées. Au point de contact avec un foret de 14 mm, nous forons des trous pour l'axe du volant. Les deux éléments sont soigneusement traités avec du papier de verre, de préférence une ponceuse orbitale. N'oubliez pas non plus de nettoyer les trous de l'axe en bois du rouleau avec du papier de verre roulé en rouleau. L'essieu doit tourner avec une résistance minimale. Les supports ainsi créés sont démontés et recouverts d'un vernis incolore.
Volant. Nous allons commencer par dessiner une structure circulaire sur du papier ordinaire.Notre volant d'inertie a un diamètre total de 200 mm et comporte six rayons. Ils seront créés de telle manière que nous dessinerons six rectangles sur le cercle, pivotés de 60 degrés par rapport à l'axe du cercle. Commençons par tracer un cercle d'un diamètre de 130 mm, puis on note les rayons d'une épaisseur de 15 mm.. Dans les coins des triangles obtenus, tracez des cercles d'un diamètre de 11 mm. Posez le papier avec la structure circulaire dessinée sur le contreplaqué et marquez d'abord les centres de tous les petits cercles et le centre du cercle avec une perforatrice. Ces empreintes assureront la précision du perçage. Dessinez un cercle, un moyeu et une roue où les rayons se terminent par une paire d'étriers, directement sur le contreplaqué. Nous forons tous les coins des triangles avec une perceuse d'un diamètre de 11 mm. Avec un crayon, marquez les endroits sur le contreplaqué qui doivent être vides. Cela nous évitera de faire des erreurs. Avec une scie sauteuse électrique ou une scie à trichome, nous pouvons couper le matériau excédentaire pré-marqué du volant, grâce auquel nous obtenons des aiguilles à tricoter efficaces. Avec une lime ou une fraise cylindrique, un décapant, puis avec une dremel, nous alignons les éventuelles imprécisions et chanfreinons les bords des rayons.
Jante de volant. Nous aurons besoin de deux jantes identiques, que nous collerons de part et d'autre du volant moteur. Nous les découperons également dans du contreplaqué de 10 mm d'épaisseur. Les roues ont un diamètre extérieur de 200 mm. Sur du contreplaqué, nous les dessinons avec un compas et les découpons avec une scie sauteuse. Ensuite, nous dessinons un cercle d'un diamètre de 130 mm coaxialement et découpons son centre. Ce sera la jante du volant, c'est-à-dire sa jante. La couronne doit augmenter l'inertie de la roue en rotation avec son poids. En utilisant de la colle wikol, nous couvrons le volant, c'est-à-dire celui avec des aiguilles à tricoter, des couronnes des deux côtés. Percez un trou de 6 mm au centre du volant moteur pour insérer une vis M6 au centre. Ainsi, on obtient un axe de rotation improvisé de la roue. Après avoir installé cette vis comme axe de la roue dans la perceuse, nous traitons rapidement la roue qui tourne, d'abord avec du papier de verre grossier puis fin. Je vous conseille de changer le sens de rotation de la perceuse pour que le boulon de roue ne se desserre pas. La roue doit avoir des bords lisses et, après traitement sur notre pseudo-tour, elle doit tourner en douceur, sans chocs latéraux. C'est un critère très important pour la qualité du volant moteur. Lorsque cet objectif est atteint, retirez le boulon provisoire et percez un trou pour l'axe d'un diamètre de 14 mm.
Cylindre de machines. Fabriqué à partir de contreplaqué de 10 mm. Nous commencerons par un haut et un bas de 140 mm x 60 mm et un arrière et un avant de 60 mm x 60 mm. Percez des trous d'un diamètre de 14 mm au centre de ces carrés. Nous collons ces éléments ensemble avec de la colle chaude d'un pistolet à colle, créant ainsi une sorte de cadre cylindrique. Les pièces à fixer doivent être perpendiculaires et parallèles entre elles, donc lors du collage, utilisez une équerre de montage et maintenez-les en place jusqu'à ce que la colle durcisse. Le rouleau qui servira de tige de piston est bien inséré dans les trous à l'arrière et à l'avant lors du collage. Le bon fonctionnement futur du modèle dépend de la précision de ce collage.
Piston. Fabriqué en contreplaqué de 10 mm d'épaisseur, a des dimensions de 60 par 60 mm. Poncez les bords du carré avec du papier de verre fin et chanfreinez les murs. Percez un trou de 14 mm dans le piston pour la tige de piston. Un trou d'un diamètre de 3 mm est percé perpendiculairement dans la partie supérieure du piston pour une vis qui fixe le piston à la tige de piston. Percez un trou avec une mèche de 8 mm pour cacher la tête de la vis. La vis traverse la tige du piston en maintenant le piston en place.
tige de piston. Découpez un cylindre d'un diamètre de 14 mm. Sa longueur est de 280 mm. Nous plaçons le piston sur la tige de piston et l'installons dans le cadre du piston. Cependant, nous déterminons d'abord la position du piston par rapport à la tige de piston. Le piston se déplacera de 80 mm. Lors du coulissement, il ne doit pas atteindre les bords des orifices d'entrée et de sortie du piston et, en position neutre, il doit se trouver au centre du cylindre et la tige du piston ne doit pas tomber de l'avant du cylindre. Lorsque nous trouvons cet endroit, nous marquons avec un crayon la position du piston par rapport à la tige de piston et enfin perçons un trou d'un diamètre de 3 mm.
Distribution. C'est la partie la plus difficile de notre voiture. Il faut recréer les conduits d'air du compresseur au cylindre, d'un côté à l'autre du piston, puis de l'air d'échappement du cylindre. Nous fabriquerons ces canaux à partir de plusieurs couches de contreplaqué de 4 mm d'épaisseur. Le chronométrage se compose de cinq plaques mesurant 140 par 80 mm. Des trous sont découpés dans chaque plaque selon les chiffres indiqués sur la photo. Commençons par dessiner sur papier les détails dont nous avons besoin et découpons tous les détails. Nous dessinons des motifs de carreaux avec un stylo-feutre sur du contreplaqué, en les disposant de manière à ne pas gaspiller de matériau, tout en ayant le moins de travail possible lors du sciage. Marquez soigneusement les emplacements marqués pour les trous auxiliaires et découpez les formes correspondantes avec une scie sauteuse ou une embase. À la fin, nous alignons tout et nettoyons avec du papier de verre.
Fermeture éclair. Il s'agit d'une planche de contreplaqué de la même forme que sur la photo. Tout d'abord, percez des trous et découpez-les avec une scie sauteuse. Le reste du matériau peut être coupé avec une scie trichome ou éliminé avec un cutter cylindrique conique ou un dremel. Sur le côté droit du curseur, il y a un trou d'un diamètre de 3 mm, dans lequel sera situé l'axe de la poignée à levier excentrique.
Glisser les guides. Le curseur fonctionne entre deux patins, les guides inférieur et supérieur. Nous les fabriquerons à partir de contreplaqué ou de lattes de 4 mm d'épaisseur et de 140 mm de long. Collez les guides avec de la colle Vicol sur la plaque de distribution suivante correspondante.
Bielle. Nous allons le couper dans une forme traditionnelle, comme sur la photo. La distance entre les axes des trous d'un diamètre de 14 mm est importante. Il doit être de 40 mm.
Manivelle. Il est fabriqué à partir d'une bande de 30 par 30 mm et a une longueur de 50 mm. Nous forons un trou de 14 mm dans le bloc et un trou borgne perpendiculaire à l'avant. Limez l'extrémité opposée du bloc avec une lime à bois et une ponceuse avec du papier de verre.
Poignée de tige de piston. Il a une forme en U, fait de bois de 30 par 30 mm et a une longueur de 40 mm. Vous pouvez voir sa forme sur la photo. Nous forons un trou de 14 mm dans le bloc sur la face avant. À l'aide d'une scie avec une lame de scie, faites deux coupes et faites une fente dans laquelle la tige de piston se déplacera, à l'aide d'une perceuse et d'une scie à trichinose. Nous forons un trou pour l'axe reliant la manivelle à la tige de piston.
Support de cylindre. Nous avons besoin de deux éléments identiques. Découpez les supports de planche de pin 90 x 100 x 20 mm.
Excentricité. Dans du contreplaqué de 4 mm d'épaisseur, découpez quatre rectangles de 40 mm x 25 mm chacun. Nous forons des trous dans les rectangles avec un foret de 14 mm. La conception de l'excentrique est montrée sur la photo. Ces trous sont situés le long de l'axe longitudinal, mais sont décalés les uns des autres le long de l'axe transversal de 8 mm. Nous connectons les rectangles en deux paires, en les collant avec leurs surfaces. Collez un cylindre de 28 mm de long dans les trous intérieurs. Assurez-vous que les surfaces des rectangles sont parallèles les unes aux autres. La poignée à levier peut nous y aider.
levierliaison du coulisseau avec l'excentrique. Il se compose de trois parties. Le premier est une poignée en forme de U qui comprend un curseur. Un trou est percé dans le plan de l'axe le long duquel il effectue un mouvement de bascule. Une pince excentrique est collée à l'autre extrémité. Ce clip est pliable et se compose de deux blocs de 20×20×50 mm chacun. Connectez les blocs avec des vis à bois, puis percez un trou de 14 mm sur le bord de la nervure pour l'axe excentrique. Perpendiculairement à l'axe dans l'un des blocs, nous forons un trou borgne d'un diamètre de 8 mm. Maintenant, nous pouvons connecter les deux pièces avec un arbre d'un diamètre de 8 mm et d'une longueur d'environ 160 mm, mais la distance entre les axes de ces pièces est importante, qui devrait être de 190 mm.
Assemblage de machines. À l'aide d'un boulon, installez le piston sur la tige de piston insérée dans le châssis du vérin et percez un trou à l'extrémité pour l'axe de la manivelle. Rappelez-vous que le trou doit être parallèle à la base. Collez les éléments d'entraînement de distribution suivants sur le châssis du cylindre (photo a). La première plaque suivante à quatre trous (photo b), la seconde à deux grands trous (photo c) relie les trous en deux paires. La suivante est la troisième plaque (photo d) avec quatre trous et placez le curseur dessus. Les photographies (photo e et f) montrent que le curseur, déplacé par l'excentrique lors du fonctionnement, expose séquentiellement l'une ou l'autre paire de trous. Collez les deux guides menant le curseur à la troisième plaque en partant du haut et du bas. Nous y attachons la dernière plaque avec deux trous, recouvrant le curseur par le haut (photo d). Collez le bloc avec le trou traversant sur le trou supérieur d'un diamètre tel que vous puissiez y fixer le tuyau d'alimentation en air comprimé. De l'autre côté, le cylindre est fermé par un couvercle vissé avec plusieurs vis. Coller les supports d'axe de volant moteur sur la base en veillant à ce qu'ils soient alignés et parallèles au plan de la base. Avant montage complet, nous peindrons les éléments et composants de la machine avec un vernis incolore. Nous plaçons la bielle sur l'axe du volant et la collons exactement perpendiculairement à celle-ci. Insérez l'axe de la bielle dans le deuxième trou. Les deux axes doivent être parallèles l'un à l'autre. De l'autre côté de la base, collez deux planches pour faire un support pour le cylindre. Nous y collons un cylindre complet avec un mécanisme de synchronisation. Une fois le cylindre collé, installez le levier qui relie le curseur à l'excentrique. Ce n'est que maintenant que nous pouvons déterminer la longueur du levier qui relie la manivelle de bielle à la tige de piston. Découpez correctement la tige et collez les poignées en forme de U. Nous connectons ces éléments avec des axes en clous. La première tentative consiste à tourner l'axe du volant à la main. Toutes les pièces mobiles doivent bouger sans résistance excessive. La manivelle fera un tour et la bobine devrait réagir avec un déplacement excentrique.
Jeu Lubrifiez la machine avec de l'huile là où vous vous attendez à ce que des frottements se produisent. Enfin, nous connectons le modèle avec un câble au compresseur. Après avoir démarré l'unité et fourni de l'air comprimé dans le cylindre, notre modèle devrait fonctionner sans problème, donnant beaucoup de plaisir au concepteur. Toute fuite peut être colmatée avec de la colle d'un pistolet à colle chaude ou du silicone transparent, mais cela rendra notre modèle indélébile. Le fait que la maquette puisse être démontée, par exemple pour montrer le mouvement d'un piston dans un cylindre, est un avantage précieux.
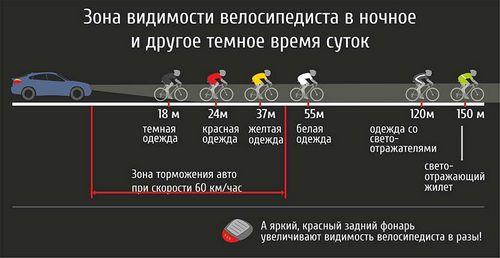
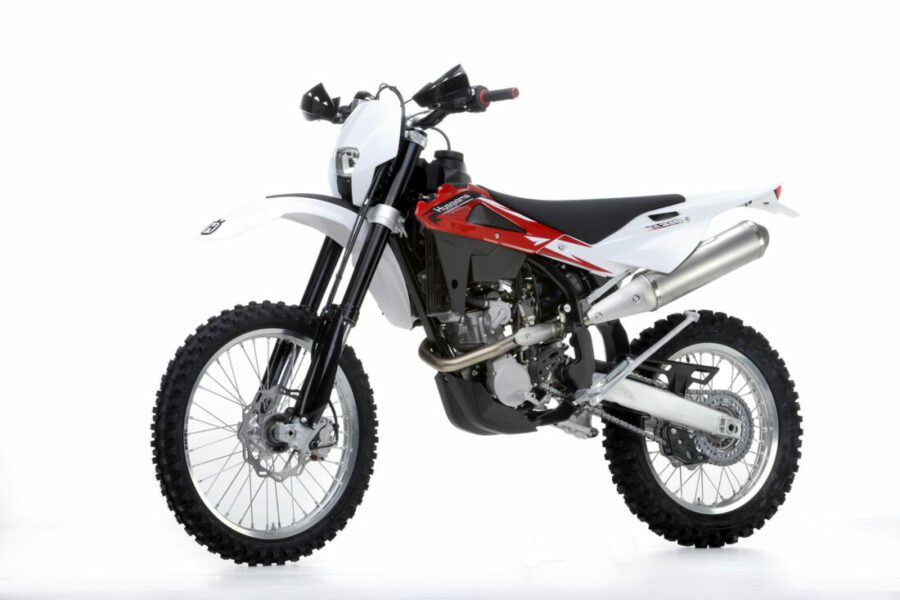