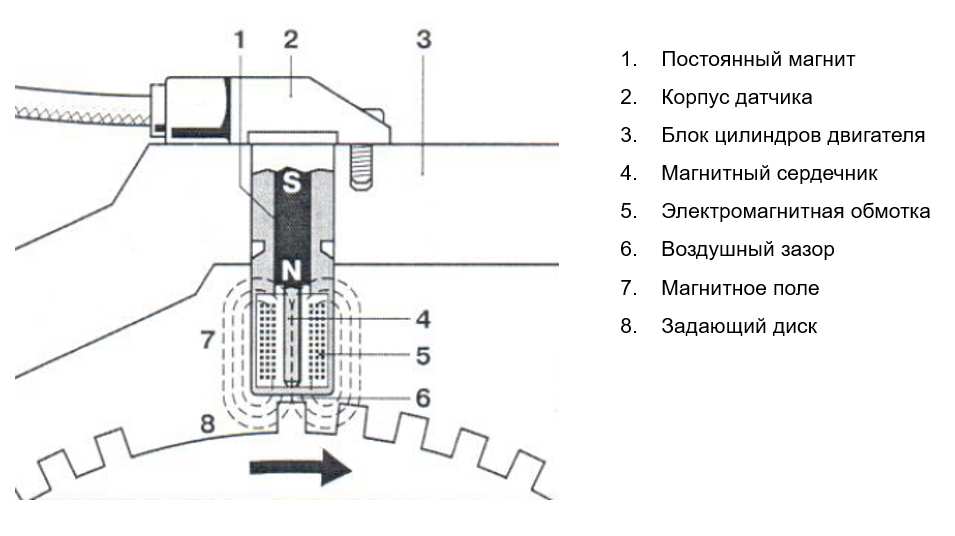
Capteur de position de vilebrequin
Teneur
Le capteur de vilebrequin permet de contrôler à partir de l'ECU du moteur la position de la pièce mécanique responsable du fonctionnement du système d'injection de carburant. Lorsque le DPKV tombe en panne, il est diagnostiqué à l'aide de testeurs spéciaux fonctionnant sur le principe d'un ohmmètre. Dans le cas où la valeur de résistance actuelle est inférieure à la valeur nominale, un remplacement du contrôleur sera nécessaire.
De quoi est responsable et comment fonctionne le capteur de vilebrequin?
Le capteur de position du vilebrequin détermine exactement quand le carburant doit être envoyé aux cylindres du moteur à combustion interne (ICE). Dans différentes conceptions, le DPKV est chargé de contrôler le réglage de l'uniformité de l'alimentation en carburant par les injecteurs.
Les fonctions du capteur de vilebrequin sont d'enregistrer et de transférer au calculateur les données suivantes :
- mesurer la position du vilebrequin;
- au moment où les pistons passent le PMB et le PMH dans les premier et dernier cylindres.
Le capteur PKV corrige les indicateurs suivants :
- la quantité de carburant entrant ;
- moment de l'approvisionnement en essence;
- angle d'arbre à cames ;
- calage de l'allumage ;
- moment et durée de fonctionnement de la vanne d'adsorption.
Le principe de fonctionnement du capteur de temps :
- Le vilebrequin est équipé d'un disque à dents (démarrage et mise à zéro). Lorsque l'ensemble tourne, le champ magnétique est dirigé vers les dents depuis le capteur PKV, agissant sur celui-ci. Les changements sont enregistrés sous forme d'impulsions et l'information est transmise à l'ordinateur : la position du vilebrequin est mesurée et le moment où les pistons passent par les points morts haut et bas (PMH et PMB) est enregistré.
- Lorsque le pignon passe devant le capteur de vitesse du vilebrequin, il change le type de lecture de suralimentation. Pour cette raison, l'ECU tente de rétablir le fonctionnement normal du vilebrequin.
- Sur la base des impulsions reçues, l'ordinateur de bord envoie un signal aux systèmes nécessaires du véhicule.
appareil DPKV
Conception du capteur de vilebrequin :
- un boîtier en aluminium ou en plastique de forme cylindrique avec un élément sensible, à travers lequel un signal est envoyé à l'ordinateur ;
- câble de communication (circuit magnétique);
- unité d'entraînement;
- mastic;
- enroulement;
- support de montage moteur.
Tableau : types de capteurs
Prénom | description |
Capteur magnétique | Le capteur se compose d'un aimant permanent et d'un enroulement central, et ce type de contrôleur ne nécessite pas d'alimentation électrique séparée. Un dispositif électrique inductif contrôle non seulement la position du vilebrequin, mais également la vitesse. Il fonctionne avec la tension qui se produit lorsqu'une dent métallique (étiquette) traverse un champ magnétique. Cela génère une impulsion de signal qui va à l'ECU. |
Capteur optique | Le capteur optique se compose d'un récepteur et d'une LED. Interagissant avec le disque d'horloge, il bloque le flux optique passant entre le récepteur et la LED. L'émetteur détecte les interruptions de lumière. Lorsque la LED traverse la zone aux dents usées, le récepteur réagit à l'impulsion et effectue la synchronisation avec l'ECU. |
Capteur de Hall | La conception du capteur comprend :
Dans un capteur de vilebrequin à effet Hall, le courant circule à l'approche d'un champ magnétique changeant. Le circuit du champ de force s'ouvre lors du passage dans des zones à dents usées et le signal est transmis à l'unité de commande électronique du moteur. Fonctionne à partir d'une source d'alimentation indépendante. |
Où se trouve le capteur ?
Emplacement du capteur de position de vilebrequin : à côté du disque entre la poulie d'alternateur et le volant moteur. Pour une connexion gratuite au réseau de bord, un câble de 50 à 70 cm de long est fourni, sur lequel se trouvent des connecteurs pour les clés. Il y a des entretoises sur la selle pour régler l'écart de 1 à 1,5 mm.
Symptômes et causes de dysfonctionnements
Symptômes d'un DPKV cassé :
- le moteur ne démarre pas ou s'arrête spontanément au bout d'un moment ;
- pas d'étincelles ;
- La détonation ICE se produit périodiquement sous des charges dynamiques;
- régime de ralenti instable ;
- la puissance du moteur et la dynamique du véhicule sont réduites ;
- lors du changement de mode, un changement spontané du nombre de tours se produit;
- regarde le voyant moteur sur le tableau de bord.
Les symptômes indiquent les raisons suivantes pour lesquelles le capteur PCV peut être défectueux :
- court-circuit entre les tours d'enroulement, distorsion possible du signal sur la position du piston au PMB et au PMH ;
- le câble reliant le DPKV à l'ECU est endommagé - l'ordinateur de bord ne reçoit pas la notification appropriée ;
- défaut de dents (éraflures, éclats, fissures), le moteur peut ne pas démarrer ;
- la pénétration de corps étrangers entre la poulie crantée et le compteur ou des dommages lors de travaux dans le compartiment moteur provoquent souvent un dysfonctionnement du DPKV.
Problèmes de démarrage du moteur
Variantes de dysfonctionnements du capteur de vilebrequin affectant le fonctionnement du moteur à combustion interne:
- Le moteur ne démarre pas. Lorsque la clé de contact est tournée, le démarreur fait tourner le moteur et la pompe à carburant bourdonne. La raison en est que l'ECU du moteur, sans recevoir de signal du capteur de position du vilebrequin, ne peut pas correctement émettre une commande: sur lequel des cylindres démarrer et sur lequel ouvrir la buse.
- Le moteur chauffe jusqu'à une certaine température et cale ou ne démarre pas en cas de gel intense. Il n'y a qu'une seule raison - une microfissure dans l'enroulement du capteur PKV.
Fonctionnement instable du moteur dans différents modes
Cela se produit lorsque le DPKV est contaminé, en particulier lorsque des copeaux de métal ou de l'huile y pénètrent. Même un léger impact sur le microcircuit magnétique du capteur de temps modifie son fonctionnement, car le compteur est très sensible.
La présence de détonation du moteur avec une charge croissante
La raison la plus courante est la défaillance du doseur, ainsi qu'une microfissure dans l'enroulement, qui se plie lors des vibrations, ou une fissure dans le boîtier, dans laquelle l'humidité pénètre.
Signes de cognement moteur :
- violation de la douceur du processus de combustion du mélange air-carburant dans les cylindres du moteur à combustion interne;
- sauter sur le récepteur ou le système d'échappement;
- échec;
- une nette réduction de la puissance du moteur.
Puissance moteur réduite
La puissance du moteur chute lorsque le mélange carburant-air n'est pas fourni à temps. La cause du dysfonctionnement est le délaminage de l'amortisseur et le déplacement de l'étoile dentée par rapport à la poulie. La puissance du moteur est également réduite en raison de dommages à l'enroulement ou au boîtier du compteur de position du vilebrequin.
Comment vérifier vous-même le capteur de vilebrequin?
Vous pouvez enquêter indépendamment sur la santé du DPKV en utilisant :
- ohmmètre;
- oscillographe;
- complexe, utilisant un multimètre, un mégohmmètre, un transformateur de réseau.
Important à savoir
Avant de remplacer l'appareil de mesure, il est également recommandé d'effectuer un diagnostic informatique complet du moteur à combustion interne. Ensuite, une inspection externe est effectuée, éliminant la contamination ou les dommages mécaniques. Et seulement après cela, ils commencent à diagnostiquer avec des appareils spéciaux.
Vérification avec un ohmmètre
Avant de procéder au diagnostic, éteignez le moteur et retirez le capteur de calage.
Instructions pas à pas pour étudier DPKV avec un ohmmètre à la maison:
- Installez un ohmmètre pour mesurer la résistance.
- Déterminez le degré de résistance de l'accélérateur (touchez les sondes du testeur aux bornes et faites-les sonner).
- La valeur acceptable est de 500 à 700 ohms.
Utilisation d'un oscilloscope
Le capteur de position du vilebrequin est vérifié avec le moteur en marche.
Algorithme d'actions à l'aide d'un oscilloscope :
- Connectez le testeur à la minuterie.
- Exécutez un programme sur l'ordinateur de bord qui surveille les lectures à partir d'un appareil électronique.
- Passer plusieurs fois un objet métallique devant le capteur de vilebrequin.
- Le multimètre est OK si l'oscilloscope réagit au mouvement. S'il n'y a pas de signaux sur l'écran du PC, il est recommandé d'effectuer un diagnostic complet.
Contrôle complet
Pour le réaliser, vous devez avoir :
- mégohmmètre ;
- transformateur de réseau;
- compteur d'inductance;
- voltmètre (de préférence numérique).
Algorithme d'actions:
- Avant de commencer une analyse complète, le capteur doit être retiré du moteur, soigneusement lavé, séché, puis mesuré. Il est effectué uniquement à température ambiante, afin que les indicateurs soient plus précis.
- Tout d'abord, l'inductance du capteur (bobine inductive) est mesurée. Sa plage de fonctionnement des mesures numériques doit être comprise entre 200 et 400 MHz.Si la valeur s'écarte fortement de la valeur spécifiée, il est probable que le capteur soit défaillant.
- Ensuite, vous devez mesurer la résistance d'isolement entre les bornes de la bobine. Pour cela, un mégohmmètre est utilisé, réglant la tension de sortie à 500 V. Il est préférable d'effectuer la procédure de mesure 2 à 3 fois pour obtenir des données plus précises. La valeur de résistance d'isolement mesurée doit être d'au moins 0,5 MΩ. Sinon, un défaut d'isolation dans la bobine peut être déterminé (y compris la possibilité d'un court-circuit entre les spires). Cela indique une panne de l'appareil.
- Ensuite, à l'aide d'un transformateur de réseau, le disque horaire est démagnétisé.
Dépannage
Il est logique de réparer le capteur pour des dysfonctionnements tels que:
- pénétration dans le capteur de pollution PKV ;
- la présence d'eau dans le connecteur du capteur ;
- rupture de la gaine de protection des câbles ou faisceaux capteurs ;
- changement de polarité des câbles de signal ;
- aucune connexion avec le harnais ;
- fils de signal courts à la masse du capteur ;
- jeu de montage réduit ou augmenté du capteur et du disque de synchronisation.
Tableau : travail avec défauts mineurs
Par défaut | Moyens |
---|---|
Pénétration à l'intérieur du capteur PKV et contamination |
|
Présence d'eau dans le connecteur du capteur |
|
Bouclier ou faisceau de câble de capteur cassé |
|
Inverser la polarité des câbles de signal |
|
Le capteur n'est pas connecté au faisceau |
|
Fils de signal de capteur court-circuités à la terre |
|
Réduire ou augmenter le jeu de montage du capteur et du disque de synchronisation |
|
Comment changer le capteur de position de vilebrequin ?
Nuances importantes à respecter lors du remplacement du DPKV:
- Avant le démontage, il est nécessaire d'appliquer des marques indiquant la position du boulon par rapport au capteur, le DPKV lui-même, ainsi que le marquage des fils et des contacts électriques.
- Lors du retrait et de l'installation d'un nouveau capteur PKV, il est recommandé de s'assurer que le disque de synchronisation est en bon état.
- Remplacez le compteur par le faisceau et le micrologiciel.
Pour remplacer le capteur PKV, vous aurez besoin de :
- nouvel appareil de mesure ;
- testeur automatique ;
- cavernomètre ;
- clé 10.
algorithme
Pour changer le capteur de position du vilebrequin de vos propres mains, vous avez besoin de:
- Éteignez le contact.
- Mettez l'appareil électronique hors tension en débranchant le bornier du contrôleur.
- Avec une clé, dévissez la vis qui fixe le capteur, retirez le DPKV défectueux.
- Utilisez un chiffon pour nettoyer le site d'atterrissage des dépôts huileux et de la saleté.
- Installez le nouveau manomètre en utilisant les anciennes fixations.
- Effectuez des mesures de contrôle de l'écart entre les dents de la poulie d'entraînement de l'alternateur et le noyau du capteur à l'aide d'un pied à coulisse. L'espace doit correspondre aux valeurs suivantes : 1,0 + 0,41 mm. Si l'écart est inférieur (supérieur) à la valeur spécifiée lors de la mesure de contrôle, la position du capteur doit être corrigée.
- Vérifier la résistance du capteur de position du vilebrequin à l'aide d'un autotest. Pour un capteur fonctionnel, il doit être compris entre 550 et 750 ohms.
- Réinitialisez l'ordinateur de bord pour désactiver le signal Check Engine.
- Connectez le capteur de position du vilebrequin au secteur (un connecteur est installé pour cela).
- Vérifier les performances de l'appareil électrique dans différents modes : au repos et sous charge dynamique.
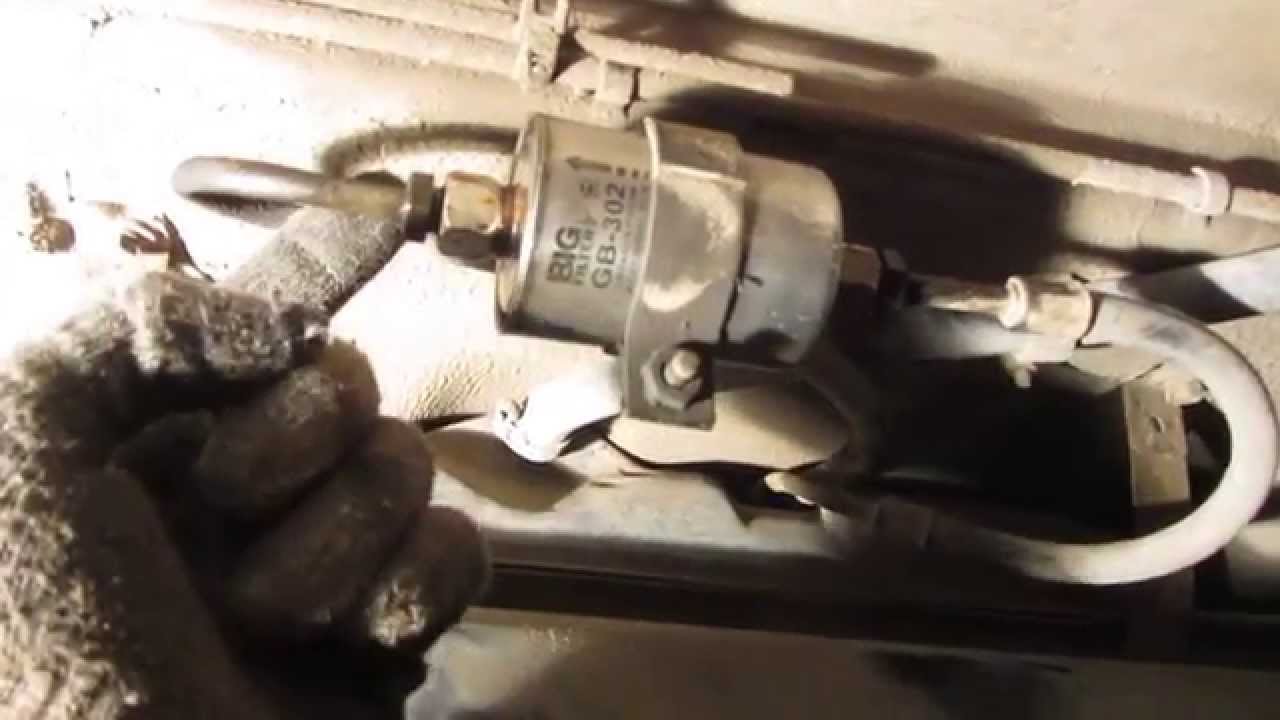
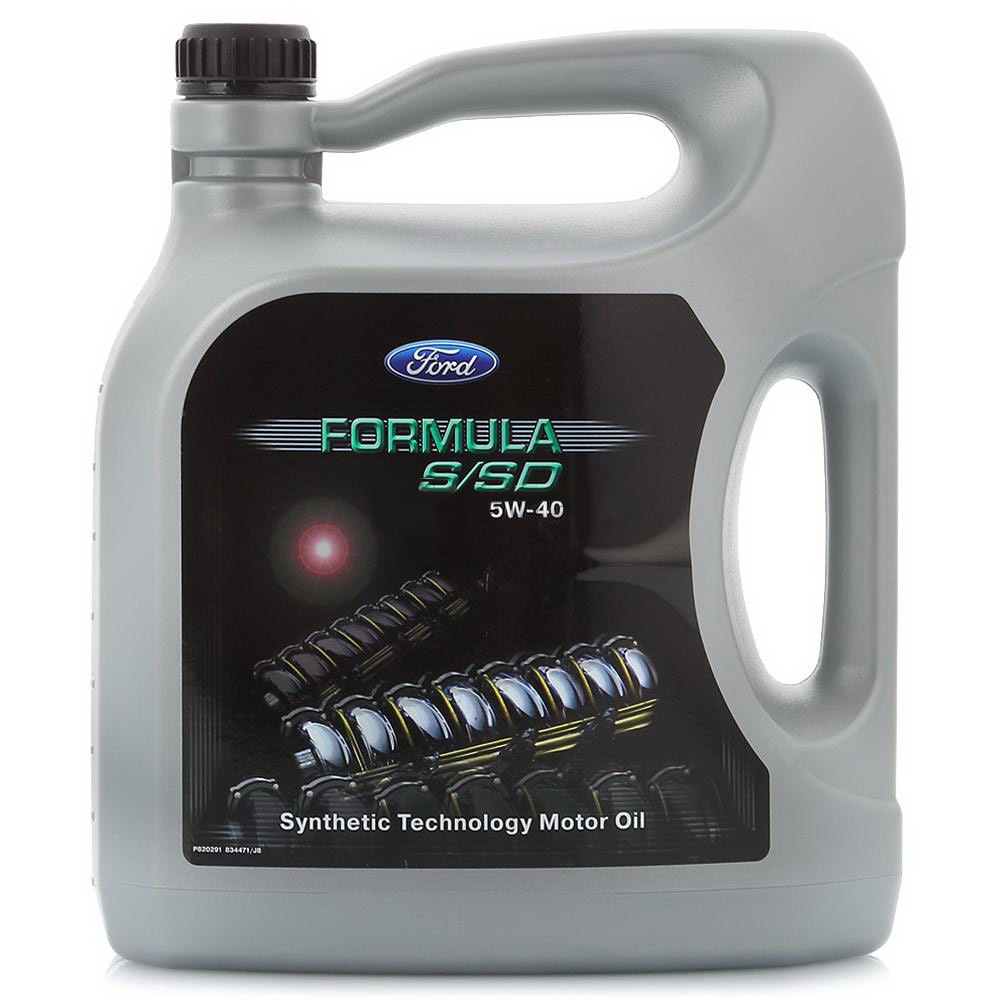