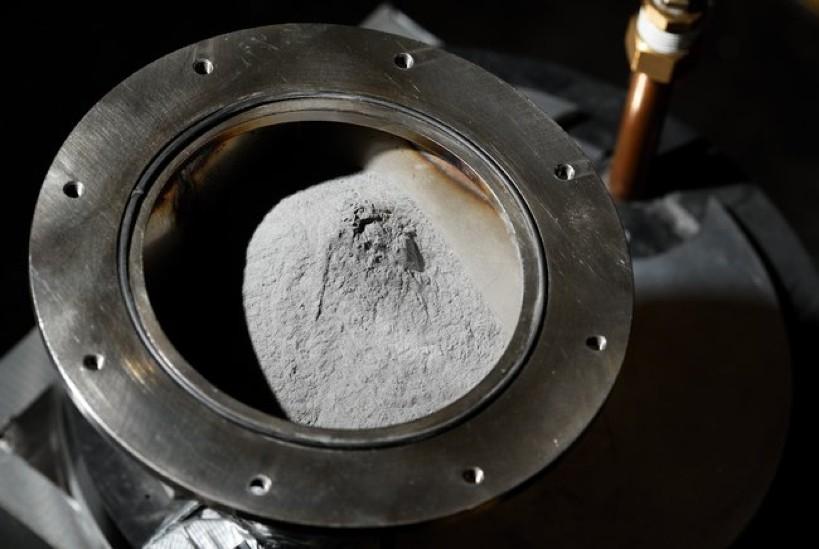
Avenir en poudre
La société suédoise VBN Components fabrique des produits en acier en utilisant des technologies additives utilisant de la poudre avec des additifs, principalement des outils tels que des perceuses et des fraises. La technologie d'impression 3D élimine le besoin de forgeage et d'usinage, réduit la consommation de matières premières et offre aux utilisateurs finaux un choix plus large de matériaux de haute qualité.
L'offre de composants VBN comprend par ex. Vibénite 290qui, selon l'entreprise suédoise, est l'acier le plus dur au monde (72 HRC). Le processus de création de Vibenite 290 consiste à augmenter progressivement la dureté des matériaux jusqu'à. Une fois que les pièces souhaitées sont imprimées à partir de cette matière première, aucun autre traitement autre que le meulage ou l'EDM n'est requis. Aucune coupe, fraisage ou perçage requis. Ainsi, l'entreprise crée des pièces de dimensions allant jusqu'à 200 x 200 x 380 mm, dont la géométrie ne peut être réalisée avec d'autres technologies de fabrication.
L'acier n'est pas toujours nécessaire. Une équipe de recherche des Laboratoires HRL a développé une solution d'impression 3D. alliages d'aluminium à haute résistance. On l'appelle méthode nanofonctionnelle. En termes simples, la nouvelle technique consiste à appliquer des poudres nanofonctionnelles spéciales sur une imprimante 3D, qui sont ensuite « frittées » avec un laser en couches minces, ce qui conduit à la croissance d'un objet tridimensionnel. Lors de la fusion et de la solidification, les structures résultantes ne sont pas détruites et conservent toute leur résistance grâce aux nanoparticules agissant comme centres de nucléation pour la microstructure prévue de l'alliage.
Les alliages à haute résistance tels que l'aluminium sont largement utilisés dans l'industrie lourde, la technologie aéronautique (par exemple le fuselage) et les pièces automobiles. La nouvelle technologie de nanofonctionnalisation leur confère non seulement une résistance élevée, mais également une variété de formes et de tailles.
Addition au lieu de soustraction
Dans les méthodes traditionnelles de travail des métaux, les déchets sont éliminés par usinage. Le processus additif fonctionne en sens inverse - il consiste à appliquer et à ajouter des couches successives d'une petite quantité de matière, créant des pièces XNUMXD de presque toutes les formes à partir d'un modèle numérique.
Bien que cette technique soit déjà largement utilisée à la fois pour le prototypage et le moulage de modèles, son utilisation directe dans la production de biens ou de dispositifs destinés au marché a été difficile en raison d'une faible efficacité et de propriétés matérielles insatisfaisantes. Cependant, cette situation évolue progressivement grâce au travail des chercheurs de nombreux centres à travers le monde.
Grâce à une expérimentation minutieuse, les deux principales technologies d'impression XNUMXD ont été améliorées : dépôt laser de métal (LMD) je fusion laser sélective (ULM). La technologie laser permet de créer avec précision des détails fins et d'obtenir une bonne qualité de surface, ce qui n'est pas possible avec l'impression par faisceau d'électrons 50D (EBM). En SLM, la pointe du faisceau laser est dirigée sur la poudre du matériau, le soudant localement selon un motif donné avec une précision de 250 à 3 microns. À son tour, LMD utilise un laser pour traiter la poudre afin de créer des structures XNUMXD autoportantes.
Ces méthodes se sont avérées très prometteuses pour la création de pièces d'avions. et, en particulier, l'application du dépôt de métal au laser élargit les possibilités de conception des composants aérospatiaux. Ils peuvent être fabriqués à partir de matériaux avec des structures internes complexes et des gradients impossibles dans le passé. De plus, les deux technologies laser permettent de créer des produits de géométrie complexe et d'obtenir des fonctionnalités étendues de produits à partir d'une large gamme d'alliages.
En septembre dernier, Airbus avait annoncé avoir équipé son A350 XWB de série de l'impression additive. support en titane, fabriqué par Arconic. Ce n'est pas fini, car le contrat d'Arconic avec Airbus prévoit l'impression 3D à partir de poudre de titane-nickel. parties du corps i Système de propulsion. Cependant, il convient de noter qu'Arconic n'utilise pas la technologie laser, mais sa propre version améliorée de l'arc électronique EBM.
L'un des jalons du développement des technologies additives dans le travail des métaux sera probablement le tout premier prototype présenté au siège du groupe néerlandais Damen Shipyards à l'automne 2017. hélice de bateau alliage métallique nommé d'après VAAMpeller. Après des tests appropriés, dont la plupart ont déjà eu lieu, le modèle a une chance d'être approuvé pour une utilisation à bord des navires.
Comme l'avenir de la technologie du travail des métaux réside dans les poudres d'acier inoxydable ou les composants en alliage, il est utile de connaître les principaux acteurs de ce marché. Selon le "Additive Manufacturing Metal Powder Market Report" publié en novembre 2017, les principaux fabricants de poudres métalliques pour l'impression 3D sont : GKN, Hitachi Chemical, Rio Tinto, ATI Powder Metals, Praxair, Arconic, Sandvik AB, Renishaw, Höganäs AB , Metaldyne Performance Group, BÖHLER Edelstahl, Carpenter Technology Corporation, Aubert & Duval.
Impression d'hélice WAAMpeller
Phase liquide
Les technologies d'additifs métalliques les plus connues reposent actuellement sur l'utilisation de poudres (c'est ainsi que la vibenite susmentionnée est créée) "frittées" et fusionnées au laser aux températures élevées requises pour le matériau de départ. Cependant, de nouveaux concepts émergent. Des chercheurs du Laboratoire de génie cryobiomédical de l'Académie chinoise des sciences de Pékin ont mis au point une méthode Impression 3D avec "encre", constitué d'un alliage métallique dont le point de fusion est légèrement supérieur à la température ambiante. Dans une étude publiée dans la revue Science China Technological Sciences, les chercheurs Liu Jing et Wang Lei démontrent une technique d'impression en phase liquide d'alliages à base de gallium, de bismuth ou d'indium avec l'ajout de nanoparticules.
Par rapport aux méthodes traditionnelles de prototypage de métal, l'impression 3D en phase liquide présente plusieurs avantages importants. Tout d'abord, un taux relativement élevé de fabrication de structures tridimensionnelles peut être atteint. De plus, ici, vous pouvez régler de manière plus flexible la température et le débit du liquide de refroidissement. De plus, le métal liquide conducteur peut être utilisé en combinaison avec des matériaux non métalliques (tels que les plastiques), ce qui élargit les possibilités de conception de composants complexes.
Des scientifiques de l'American Northwestern University ont également développé une nouvelle technique d'impression 3D métal qui est moins chère et moins complexe que celle connue auparavant. Au lieu de poudre métallique, de lasers ou de faisceaux d'électrons, il utilise four conventionnel i matière liquide. De plus, la méthode fonctionne bien pour une grande variété de métaux, alliages, composés et oxydes. Il est similaire au joint de buse tel que nous le connaissons avec les plastiques. "L'encre" consiste en une poudre métallique dissoute dans une substance spéciale avec l'ajout d'un élastomère. Au moment de l'application, il est à température ambiante. Après cela, la couche de matériau déposée à partir de la buse est frittée avec les couches précédentes à une température élevée créée dans le four. La technique est décrite dans la revue spécialisée Advanced Functional Materials.
Méthode d'impression chinoise en phase de métal liquide
En 2016, des chercheurs de Harvard ont introduit une autre méthode permettant de créer des structures métalliques en XNUMXD. imprimé "dans l'air". L'Université de Harvard a créé une imprimante 3D qui, contrairement à d'autres, ne crée pas d'objets couche par couche, mais crée des structures complexes "dans l'air" - à partir de métal instantanément gelé. L'appareil, développé à la John A. Paulson School of Engineering and Applied Sciences, imprime des objets à l'aide de nanoparticules d'argent. Le laser focalisé chauffe le matériau et le fusionne, créant diverses structures telles qu'une hélice.
La demande du marché pour les produits grand public imprimés en 3D de haute précision tels que les implants médicaux et les pièces de moteur d'avion augmente rapidement. Et parce que les données produit peuvent être partagées avec d'autres, les entreprises du monde entier, si elles ont accès à la poudre métallique et à la bonne imprimante 3D, peuvent s'efforcer de réduire les coûts de logistique et d'inventaire. Comme on le sait, les technologies décrites facilitent grandement la fabrication de pièces métalliques de géométrie complexe, en avance sur les technologies de production traditionnelles. Le développement d'applications spécialisées est susceptible d'entraîner une baisse des prix et une ouverture à l'utilisation de l'impression 3D dans des applications conventionnelles également.
L'acier suédois le plus dur - pour l'impression 3D :
L'acier le plus dur au monde - fabriqué à Uppsala, en Suède
Film d'aluminium pour l'impression :
Percée dans la métallurgie : impression 3D d'aluminium à haute résistance

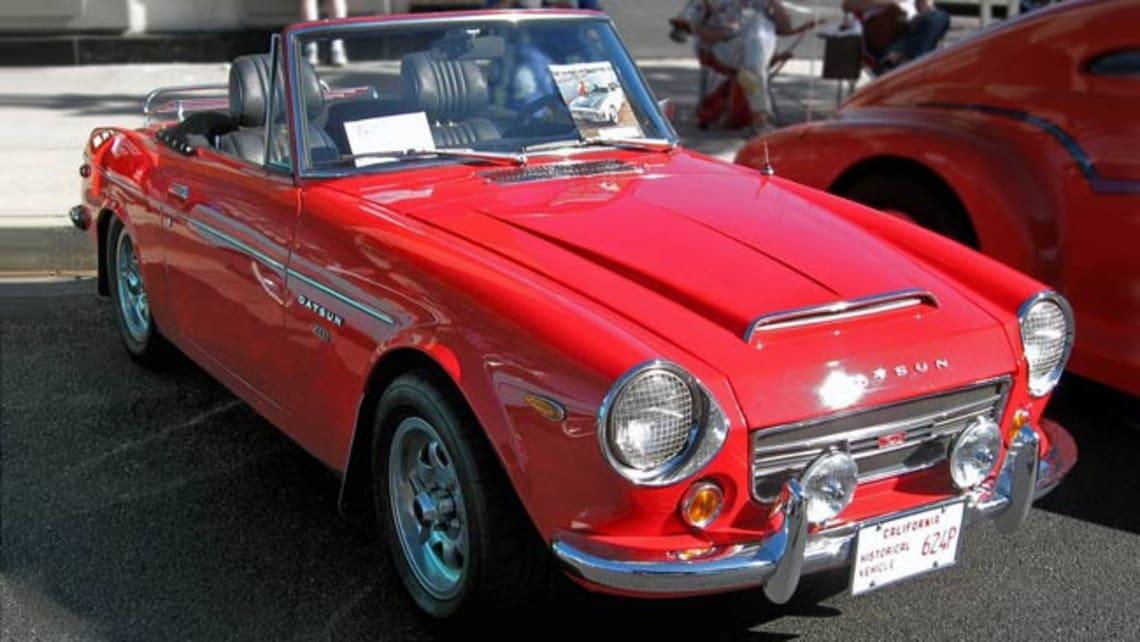
Un commentaire
anonyme
Astuce