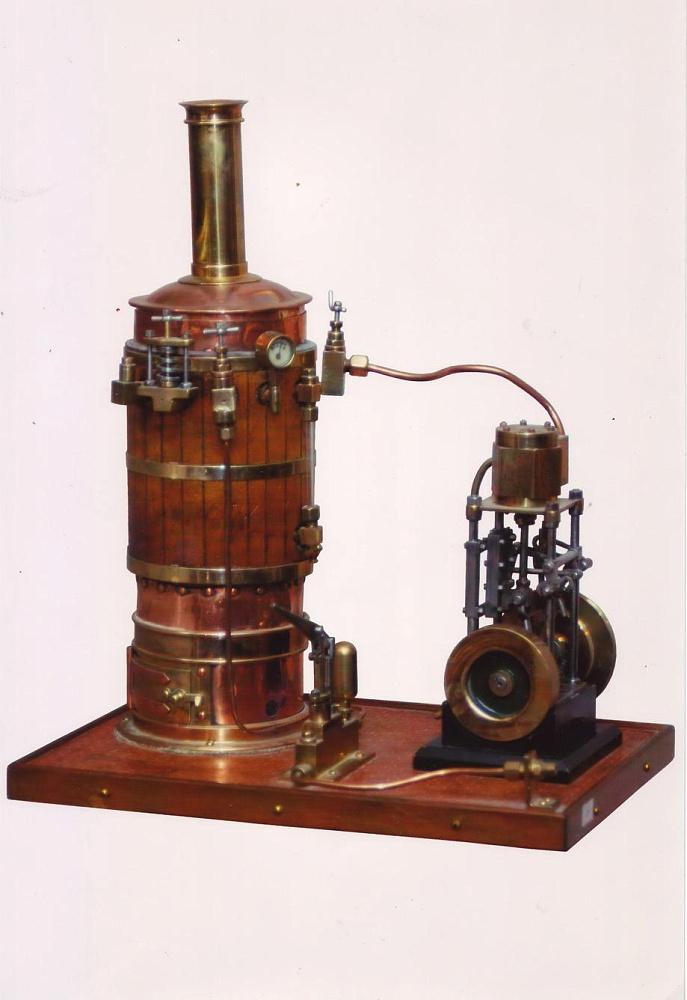
machine à vapeur en bois
Les premières machines à vapeur à cylindre oscillant mobile ont été créées au XIXe siècle et servaient à propulser de petits navires à vapeur. Leurs avantages incluent la simplicité de construction. Bien sûr, ces machines à vapeur n'étaient pas en bois, mais en métal. Ils avaient peu de pièces, ils ne tombaient pas en panne et ils étaient bon marché à fabriquer. Ils ont été fabriqués en version horizontale ou verticale afin qu'ils ne prennent pas beaucoup de place sur le navire. Ces types de moteurs à vapeur étaient également produits sous forme de miniatures fonctionnelles. C'étaient des jouets polytechniques à vapeur.
La simplicité de conception de la machine à vapeur à cylindre oscillant est son grand avantage, et l'on peut être tenté de réaliser un tel modèle en bois. Nous voulons certainement que notre modèle fonctionne et ne reste pas immobile. C'est réalisable. Cependant, nous ne le conduirons pas avec de la vapeur chaude, mais avec de l'air froid ordinaire, de préférence d'un compresseur domestique ou, par exemple, d'un aspirateur. Le bois est un matériau intéressant et facile à travailler, vous pouvez donc y recréer le mécanisme d'une machine à vapeur. Depuis lors de la construction de notre modèle, nous avons prévu la partie latérale du cylindre, grâce à cela, nous pouvons voir comment fonctionne le piston et comment le cylindre se déplace par rapport aux trous de calage. Je vous suggère de vous mettre immédiatement au travail.
Fonctionnement de la machine vapeur avec un cylindre basculant. Nous pouvons les analyser pour Photo 1 sur une série de photographies notées de a à f.
- La vapeur pénètre dans le cylindre par l'entrée et pousse le piston.
- Le piston fait tourner le volant à travers la tige de piston et la manivelle de bielle.
- Le cylindre change de position, au fur et à mesure que le piston se déplace, il ferme l'entrée et ouvre la sortie de vapeur.
- Le piston, entraîné par l'inertie du volant d'accélération, pousse la vapeur d'échappement à travers ce trou, et le cycle recommence.
- Le cylindre change de position et l'admission s'ouvre.
- La vapeur comprimée passe à nouveau par l'entrée et pousse le piston.
Outils: Perceuse électrique sur pied, perceuse fixée sur établi, ponceuse à bande, meuleuse vibrante, dremel avec pointes à bois, scie sauteuse, machine à encoller à chaud, filière M3 avec mandrin à fileter, perceuse de menuiserie 14 millimètres. Nous utiliserons un compresseur ou un aspirateur pour piloter le modèle.
Matériaux: planche de pin de 100 sur 20 millimètres de large, rouleau de 14 millimètres de diamètre, planche de 20 sur 20 millimètres, planche de 30 sur 30 millimètres, planche de 60 sur 8 millimètres, contreplaqué de 10 millimètres d'épaisseur. De la graisse de silicone ou de l'huile de machine, un clou d'un diamètre de 3 millimètres et d'une longueur de 60 millimètres, un ressort solide, un écrou avec une rondelle M3. Vernis incolore en bombe aérosol pour le vernissage du bois.
Base de la machine. Nous allons le fabriquer à partir d'une planche mesurant 500 par 100 par 20 millimètres. Avant de peindre, il est bon de niveler toutes les irrégularités de la planche et les endroits laissés après la découpe avec du papier de verre.
Support volant. Nous l'avons découpé dans une planche de pin mesurant 150 sur 100 sur 20 millimètres. Nous avons besoin de deux éléments identiques. Après avoir arrondi avec une ponceuse à bande, du papier de verre 40 le long des bords supérieurs dans les arcs et un traitement avec du papier de verre fin dans les supports, percez des trous d'un diamètre de 14 millimètres aux endroits indiqués sur la fig. Photo 2. La hauteur du chariot entre la base et l'essieu doit être supérieure au rayon du volant.
Jante de volant. Nous le découperons dans du contreplaqué de 10 millimètres d'épaisseur. La roue a un diamètre de 180 millimètres. Dessinez deux cercles identiques sur le contreplaqué avec un pied à coulisse et découpez-les avec une scie sauteuse. Sur le premier cercle, tracez un cercle d'un diamètre de 130 millimètres coaxialement et découpez son centre. Ce sera la jante du volant, c'est-à-dire sa jante. Une couronne pour augmenter l'inertie d'un rouet.
Volant. Notre volant a cinq rayons. Ils seront créés de manière à dessiner cinq triangles sur la roue avec des bords arrondis et une rotation de 72 degrés par rapport à l'axe de la roue. Commençons par dessiner un cercle d'un diamètre de 120 millimètres sur papier, suivi d'aiguilles à tricoter de 15 millimètres d'épaisseur et de cercles aux coins des triangles obtenus. Vous pouvez le voir sur Photo 3. i 4., où le design de la roue est représenté. Nous posons le papier sur les cercles découpés et marquons les centres de tous les petits cercles avec une perforatrice. Cela garantira la précision du forage. Nous forons tous les coins des triangles avec une perceuse d'un diamètre de 14 millimètres. Étant donné qu'une perceuse à lame peut endommager le contreplaqué, il est recommandé de ne percer que la moitié de l'épaisseur du contreplaqué, puis de retourner le matériau et de terminer le perçage. Un foret plat de ce diamètre se termine par un minuscule arbre saillant qui nous permettra de localiser avec précision le centre du trou percé de l'autre côté du contreplaqué. En réfléchissant à la supériorité des perceuses cylindriques de menuiserie sur la menuiserie plate, nous avons coupé le matériau inutile restant du volant avec une scie sauteuse électrique pour obtenir des aiguilles à tricoter efficaces. Dremel compense les imprécisions et arrondit les bords des rayons. Collez le cercle de la couronne avec de la colle vicola. Nous forons un trou d'un diamètre de 6 millimètres au centre afin d'y insérer une vis M6 au centre, obtenant ainsi un axe de rotation approximatif de la roue. Après avoir installé le boulon comme axe de la roue dans la perceuse, nous traitons la roue à rotation rapide, d'abord avec du papier de verre à grain grossier, puis avec du papier de verre fin. Je vous conseille de changer le sens de rotation de la perceuse pour que le boulon de roue ne se desserre pas. La roue doit avoir des bords réguliers et tourner uniformément après le traitement, sans heurter le côté. Lorsque cela est réalisé, nous démontons le boulon temporaire et perçons un trou pour l'axe cible d'un diamètre de 14 millimètres.
Bielle. Nous le découperons dans du contreplaqué de 10 millimètres d'épaisseur. Pour faciliter le travail, je suggère de commencer par percer deux trous de 14 mm à 38 mm d'intervalle, puis de scier la forme classique finale, comme indiqué dans Photo 5.
axe de volant. Il est composé d'un arbre d'un diamètre de 14 millimètres et d'une longueur de 190 millimètres.
Axe d'arbre. Il est taillé dans une tige d'un diamètre de 14 millimètres et d'une longueur de 80 millimètres.
Cylindre Nous le découperons dans du contreplaqué de 10 millimètres d'épaisseur. Il se compose de cinq éléments. Deux d'entre eux mesurent 140 par 60 millimètres et constituent les parois latérales du cylindre. Bas et haut 140 par 80 millimètres. La partie inférieure du cylindre mesure 60 par 60 et fait 15 millimètres d'épaisseur. Ces pièces sont présentées dans Photo 6. Nous collons le fond et les côtés du cylindre avec de la colle tressée. L'une des conditions du bon fonctionnement du modèle est la perpendicularité du collage des parois et du fond. Percez des trous pour les vis dans la partie supérieure du couvercle du cylindre. Nous forons des trous avec un foret de 3 mm afin qu'ils tombent au centre de l'épaisseur de paroi du cylindre. Percez un peu les trous dans le couvercle avec un foret de 8 mm afin que les têtes de vis puissent se cacher.
Piston. Ses dimensions sont de 60 par 60 par 30 millimètres. Dans le piston, nous forons un trou borgne central d'un diamètre de 14 millimètres sur une profondeur de 20 millimètres. Nous y insérerons la tige de piston.
Tige de piston. Il est composé d'un arbre d'un diamètre de 14 millimètres et d'une longueur de 320 millimètres. La tige de piston se termine d'un côté par un piston, et de l'autre côté par un crochet sur l'axe de la manivelle de bielle.
Axe de bielle. Nous allons le fabriquer à partir d'une barre d'une section de 30 par 30 et d'une longueur de 40 millimètres. Nous forons un trou de 14 mm dans le bloc et un deuxième trou borgne perpendiculaire à celui-ci. Nous allons coller l'autre extrémité libre de la tige de piston dans ce trou. Nettoyez l'intérieur du trou traversant et poncez-le avec du papier de verre fin roulé dans un tube. L'axe de la bielle tournera dans l'alésage et nous voulons réduire la friction à ce point. Enfin, le manche est arrondi et fini avec une lime à bois ou une ponceuse à bande.
Support de synchronisation. Nous allons le découper dans une planche de pin mesurant 150 par 100 par 20. Après avoir poncé dans le support, percez trois trous aux endroits indiqués sur la photo. Le premier trou d'un diamètre de 3 mm pour l'axe de synchronisation. Les deux autres sont l'entrée et la sortie d'air du cylindre. Le point de forage pour les trois est indiqué dans Photo 7. Lors de la modification des dimensions des pièces de la machine, les emplacements de perçage doivent être trouvés de manière empirique en pré-assemblant la machine et en déterminant les positions supérieure et inférieure du cylindre, à savoir l'emplacement du trou percé dans le cylindre. L'endroit où le chronométrage fonctionnera est poncé avec une ponceuse orbitale avec du papier fin. Il doit être uniforme et très lisse.
Axe de distribution oscillant. Émoussez le bout d'un clou de 60 mm de long et arrondissez-le avec une lime ou une meuleuse. À l'aide d'une matrice M3, coupez son extrémité d'environ 10 millimètres de long. Pour ce faire, choisissez un ressort solide, un écrou et une rondelle M3.
Distribution. Nous allons le fabriquer à partir d'une bande mesurant 140 par 60 par 8 millimètres. Deux trous sont percés dans cette partie du modèle. Le premier mesure 3 millimètres de diamètre. Nous y mettrons un clou, qui est l'axe de rotation du cylindre. N'oubliez pas de percer ce trou de manière à ce que la tête du clou soit complètement enfoncée dans le bois et ne dépasse pas de sa surface. C'est un moment très important dans notre travail, affectant le bon fonctionnement du modèle. Le deuxième trou de 10 mm de diamètre est l'entrée/sortie d'air. En fonction de la position du cylindre par rapport aux trous du support de distribution, l'air pénètre dans le piston, le pousse, puis est expulsé par le piston dans la direction opposée. Collez le calage avec le clou collé qui sert d'axe à la surface du cylindre. L'axe ne doit pas vaciller et doit être perpendiculaire à la surface. Enfin, percez un trou dans le cylindre en utilisant l'emplacement du trou dans le tableau de distribution. Toutes les irrégularités du bois, là où il sera en contact avec le support de calage, sont lissées avec une ponceuse orbitale à papier de verre fin.
Assemblage de machines. Coller les supports d'axe de volant moteur sur la base en veillant à ce qu'ils soient alignés et parallèles au plan de la base. Avant montage complet, nous peindrons les éléments et composants de la machine avec un vernis incolore. Nous plaçons la bielle sur l'axe du volant et la collons exactement perpendiculairement à celle-ci. Insérez l'axe de la bielle dans le deuxième trou. Les deux axes doivent être parallèles l'un à l'autre. Collez des anneaux de renforcement en bois sur le volant. Dans la bague extérieure, insérez une vis à bois dans le trou qui fixe le volant à l'axe du volant. De l'autre côté de la base, collez le support du cylindre. Lubrifiez toutes les pièces en bois qui bougent et entrent en contact les unes avec les autres avec de la graisse silicone ou de l'huile pour machine. Le silicone doit être légèrement poli pour minimiser les frottements. Le bon fonctionnement de la machine en dépendra. Le cylindre est monté sur le chariot de manière à ce que son axe dépasse du calage. Vous pouvez le voir sur Photo 8. Mettez le ressort sur le clou dépassant du support, puis la rondelle et fixez le tout avec un écrou. Le cylindre, pressé par un ressort, doit se déplacer légèrement sur son axe. Nous mettons le piston à sa place dans le cylindre et plaçons l'extrémité de la tige de piston sur l'axe de la bielle. Nous posons le couvercle du cylindre et le fixons avec des vis à bois. Lubrifiez toutes les pièces coopérantes du mécanisme, en particulier le cylindre et le piston, avec de l'huile pour machine. Ne regrettons pas le gras. La roue déplacée à la main doit tourner sans aucune résistance ressentie et la bielle doit transférer le mouvement au piston et au cylindre. Photo 9. Insérez l'extrémité du tuyau du compresseur dans l'entrée et allumez-le. Tournez la roue et l'air comprimé déplacera le piston et le volant commencera à tourner. Le point critique de notre modèle est le contact entre la plaque de distribution et son stator. À moins que la majeure partie de l'air ne s'échappe de cette façon, une voiture bien conçue devrait se déplacer facilement, ce qui procurera beaucoup de plaisir aux bricoleurs. La cause du dysfonctionnement peut être un ressort trop faible. Au bout d'un moment, l'huile pénètre dans le bois et le frottement devient trop important. Cela explique également pourquoi les gens n'ont pas construit de machines à vapeur en bois. Cependant, le moteur en bois est très efficace et la connaissance du fonctionnement du cylindre oscillant dans une machine à vapeur aussi simple reste longtemps.
machine à vapeur en bois
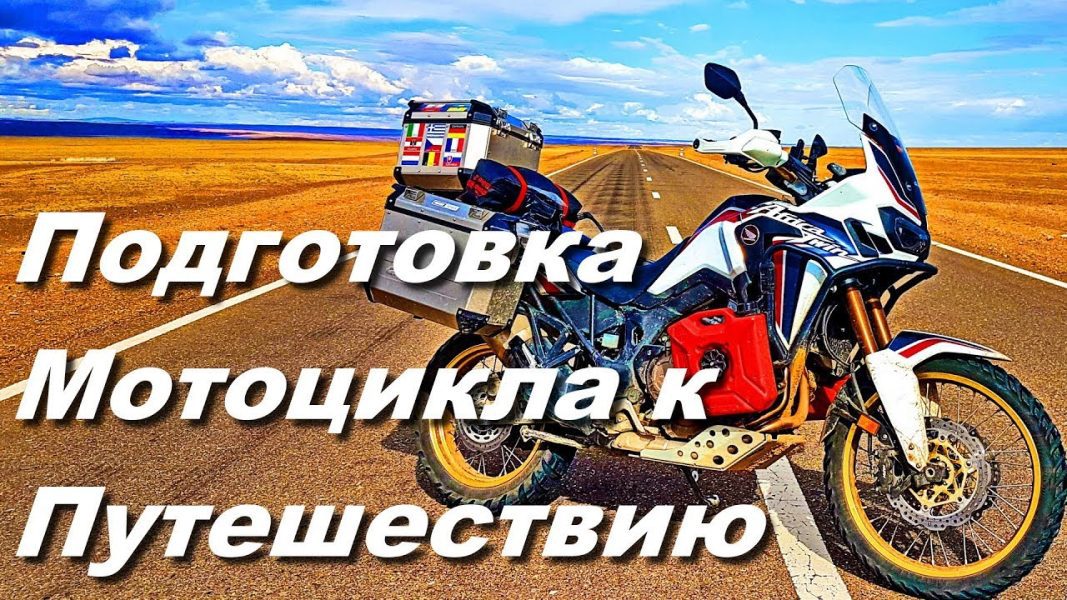
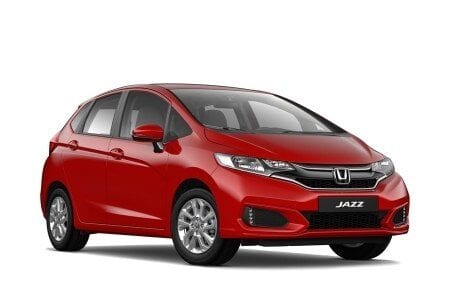